(2) 5
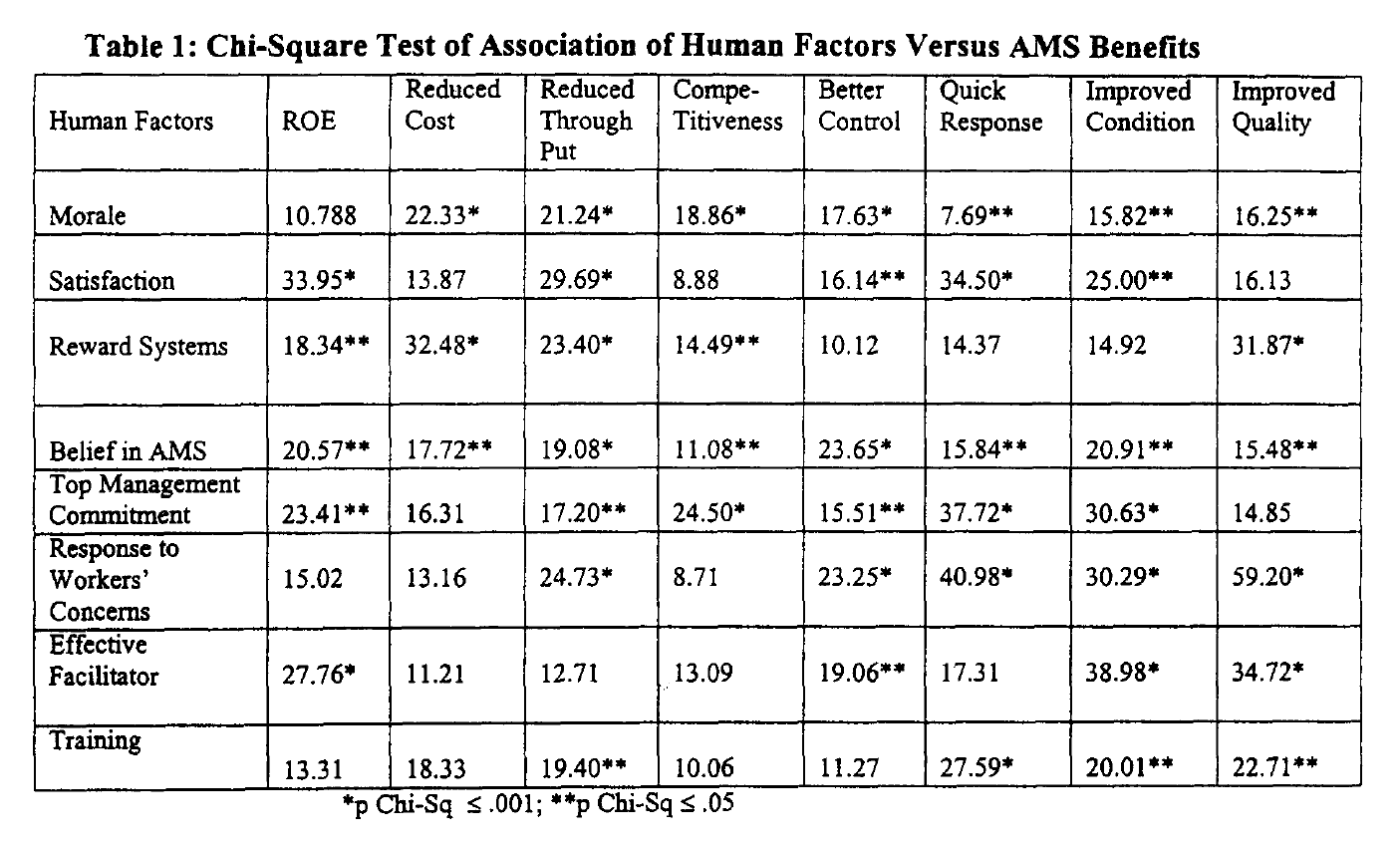
RESEARCH METHOD AND RESULTS
This study utilized a survey instrument on the U.S. manufacturing firms who were most likely to adopt AMS. The firms were selected from the following three publications: Moody's Industrial Manual, American Association of Manufacturing Technology (AAMT), and A.MS trade journals. Within each firm, a plant manager was identified as target for the questionnaire. To ensure an appropriate level of respondent knowledge, only participants meeting the following criteria were included in the study: (1) at least six months of AMS use by the organization, and (2) at least six months AMS experience by the individual participant. Those respondents that did not meet these conditions were asked to so indicate and return the questionnaire. This action ensured that each participant was familiar with and able to objectively evaluate the AMS adopted in his/her organization. The respondents were urged to take part in the study only if the requirements stated above were met.
Of the 400 questionnaires mailed out, we received 117 responses (29.3 percent). Nineteen were discarded, eight because they were not completely filled out and eleven because the respondents indicated insufficient experience with AMS. There remained 92 (23 percent) usable responses that were included in the study.
Human factors were investigated by asking respondents to indicate the extent to which they felt the eight human factors discussed earlier were present during and after AMS implementation. Over 37% of the participating firms had a process manufacturing environment while about 30% operated in a repetitive manufacturing environment. The respondents reported that A_MS projects were initiated mostly (over 80%) by management rather than workers or vendors. In about 80% of the cases, the AMS projects were directed by management rather than a steering committee or appointed individuals. Over 38% of the respondents were top management, 38.5% were middle management, and about 19% belonged to other ranks.
The Partial correlation coefficients of the human factors and AMS benefit measures were computed. According to the results, the benefit measures did not indicate any multi-collinearity problem. The Partial Coefficients (r) of 0.1900 or higher are significant at p < .06. The correlation analysis reveals that all human factors positively correlate the benefit measures. The strongest correlation were found between morale and reduced throughput time (r = .4318; p < .000); satisfaction and return on equity (r = .2026, p < .060); reward system and reduced throughput time (r = .3274, p < .002); belief in AMS and improved work conditions (r = .3651, p < .001); top management commitment and enhanced competitiveness (r = .3714, p < .000); response to workers' concerns and better control (r = .3453, p < .001); effective facilitator and better control (r = .2483, p ~ .020); training and improved quality (r = .2305, p < .011).
Table 1 is a record of the Chi-Square test obtained by cross-tabulating human factors and AMS benefit measures. The association between any two variables was significant if p _< .001 (*) or p< .05 (**). In order to test the hypotheses of the study, Chi Square testes were conducted to determine if there exist any associations between human factors and the benefits of AMS. As shown on Table 1, every human factor considered in this study has significant association with some of the AMS benefits measures.
Of the 400 questionnaires mailed out, we received 117 responses (29.3 percent). Nineteen were discarded, eight because they were not completely filled out and eleven because the respondents indicated insufficient experience with AMS. There remained 92 (23 percent) usable responses that were included in the study.
Human factors were investigated by asking respondents to indicate the extent to which they felt the eight human factors discussed earlier were present during and after AMS implementation. Over 37% of the participating firms had a process manufacturing environment while about 30% operated in a repetitive manufacturing environment. The respondents reported that A_MS projects were initiated mostly (over 80%) by management rather than workers or vendors. In about 80% of the cases, the AMS projects were directed by management rather than a steering committee or appointed individuals. Over 38% of the respondents were top management, 38.5% were middle management, and about 19% belonged to other ranks.
The Partial correlation coefficients of the human factors and AMS benefit measures were computed. According to the results, the benefit measures did not indicate any multi-collinearity problem. The Partial Coefficients (r) of 0.1900 or higher are significant at p < .06. The correlation analysis reveals that all human factors positively correlate the benefit measures. The strongest correlation were found between morale and reduced throughput time (r = .4318; p < .000); satisfaction and return on equity (r = .2026, p < .060); reward system and reduced throughput time (r = .3274, p < .002); belief in AMS and improved work conditions (r = .3651, p < .001); top management commitment and enhanced competitiveness (r = .3714, p < .000); response to workers' concerns and better control (r = .3453, p < .001); effective facilitator and better control (r = .2483, p ~ .020); training and improved quality (r = .2305, p < .011).
Table 1 is a record of the Chi-Square test obtained by cross-tabulating human factors and AMS benefit measures. The association between any two variables was significant if p _< .001 (*) or p< .05 (**). In order to test the hypotheses of the study, Chi Square testes were conducted to determine if there exist any associations between human factors and the benefits of AMS. As shown on Table 1, every human factor considered in this study has significant association with some of the AMS benefits measures.
CONCLUSIONS
The dramatic advancement and the adoption of advanced manufacturing systems (AMS) in organizations can be attributed to its numerous benefits that can improve the competitive position of the manufacturing firms. The results of this study show that the eight human factors considered in this study have positive associations with all the eight AMS benefits. While other factors may play major roles in realization of AMS benefits, sociotechnical or human factors have been shown to be essential ingredients for AMS success. For a manufacturing firm to actualize the full benefits of AMS, steps need to be taken to ensure effective human resource management. The implication is that when a firm takes care of the human needs, the AMS implementation will be well received and understood and as such, the desired effects of AMS will be brought to bear in the firm's production cost. In essence, the manufacturing firm that pays attention to human factors may realize the benefit of shorter throughput time because AMS is properly implemented and efficiently operated. If human factors are ignored in a firm during AMS implementation, there is a good chance that the workers will be discouraged and reluctant to apply themselves and as such, delays may occur in the production schedules. If that is the case, components of the manufacturing system will not be interacting in the most efficient way thereby resulting in a long throughput time.